Study on Optimization of spiral milling process for large diameter holes of TC4 titanium alloy parts
Based on the spiral milling technology, the spiral milling test of 19.05mm diameter hole was carried out on titanium alloy parts by orthogonal test and extreme difference analysis method. The effects of different cutting parameters on axial cutting force, titanium alloy aperture and roughness were analyzed, and the optimal process parameters were optimized as indicators. On this basis, the variation of cutting force, machining quality and tool wear with the number of holes is studied under the optimum parameters. It is found that in the processing of large diameter holes, the spiral milling technology can effectively improve the processing quality and improve the processing efficiency.
With the development of the aerospace industry, the application of titanium alloys has become more and more extensive, and the requirements for hole making precision and surface quality are getting higher and higher. At present, titanium alloy is not only an indispensable metal material in the aerospace industry, but also widely used in medical equipment and tools, metallurgy, shipbuilding and other industries. However, the titanium alloy has high strength, high hardness, low thermal conductivity, and the heat of cutting is not easily dissipated, resulting in serious tool wear, which seriously affects the service life of the tool, and the surface quality is poor and the efficiency is low. The tool movement during spiral milling is composed of three aspects: tool rotation, revolution and axial feed. The tool center is in a spiral path and is a process of drilling with a belt to facilitate chip discharge and heat dissipation (see Figure 1). This technology can greatly reduce the axial force, improve the quality of hole-making and improve the efficiency of hole-making. It can also easily realize "one knife and multi-path" by adjusting the eccentricity, which is favored by the aviation industry.
Kangding Company studied the special tool for spiral milling based on the principle of chipping, and analyzed the chipping effect of the special tool, the different cutting action of the end and side cutting edges and the service life of the tool. Perform finite element two-dimensional simulation of tools with different angle parameters to determine the appropriate tool angle range. The special tool for spiral milling is designed, and the dynamics of the spiral milling hole is studied. E.A. Rahim studied the effect of tool edge on the performance of the milling cutter. Jamal Ahnmad pointed out that the back angle of the spiral milling tool has a great influence on the cutting force. The cogging spiral milling cutter studied by Chatelian et al. has good cutting performance. The CFRP/Ti6Al4V process was studied, and the technological advantages of large pitch milling hole for processing laminated components were put forward. Li Dengwan optimized the processing parameters of titanium alloy by uniform design method, and improved cutting efficiency and surface quality. Chen Ertao established a machining parameter optimization model based on cutting parameters such as cutting speed, depth of cut and feed per tooth. Wang Fengchao studied the effects of different cutting parameters on the burr height, pore diameter deviation and roughness of the outlet.
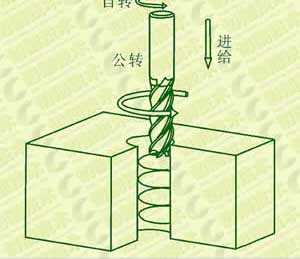
figure 1 Schematic diagram of TC4 titanium alloy spiral milling hole
In the assembly of aircraft, the number of holes below 1/2" diameter is the largest, so the research on spiral milling technology is mostly concentrated here. However, there are a certain number of large diameter holes in the key bearing parts, which is very difficult to process. At present, large-diameter hole processing usually uses multiple processes such as drilling, expanding, and reaming. The process is complicated, it requires dozens of tools, the processing cost is high, and the processing efficiency is extremely low, which has always been one of the difficulties in aircraft assembly.
Take a 12mm diameter spiral milling cutter as an example. The method of orthogonal milling and extreme value analysis was used to study the 19.05mm (3/4") large diameter spiral milling process of titanium alloy. The influence of different parameters on the processing quality was analyzed, and the optimal processing parameters were optimized. The research is beneficial to promote the application of spiral milling holes in the processing of large diameter holes, and it is also important to improve the efficiency of aircraft assembly and reduce the processing cost.
1. Test equipment and test design
1.1 Test equipment and materials
The tool used in the test was an uncoated hard alloy spiral milling tool: The diameter is 12mm, the machining aperture is 19.05mm, the helix angle is 35°, the rake angle is 8°, the back angle is 15°, and the number of cutting edges is 4. The dry cutting method is adopted. The test workpiece material is a titanium alloy sheet with a thickness of 5 mm and a size of 120×250 mm. The physical properties and mechanical properties of titanium alloy are shown in Table 1.
The machining center is DMC75Vlinear five-axis CNC machine tool. The cutting force was measured by a three-way Kistler 9257A dynamometer. The detected signal is transmitted by Kistler 5007A charge amplifier, collected by data acquisition card, and displayed in real time by Dynoware dynamometer software. Aperture detection was performed using a Wenzel LH65 coordinate measuring machine, and four-point sampling was performed for each well to obtain aperture data; The roughness measurement was performed using a Mitutoyo roughness tester, and the tool wear was observed with an ultra depth microscope.
Table 2 DMC75Vlinear five-axis CNC machine tool orthogonal experimental parameter table
1.2 Ti-6Al-4V process cutting test design
Machining 3/4 (19.05 mm) holes with 12 mm large diameter cutter. The specific experimental parameters of three-factor and three-level orthogonal test are shown in Table 2. Among them, the pitch represents the downward feed distance of the tool per revolution, and the tangential feed per tooth represents the tangential cutting thickness of each cutting edge. Two wells were processed in each set of experiments and the measured parameters were averaged.
2. Test Results And Analysis
2.1 The influence of different processing parameters on cutting force
FIG 2 is a variation of the fifth set of cutting parameters measured under the condition of three-time curve of the cutting force, the axial cutting force is defined as the z-axis direction. It can be seen from the figure that the fluctuation trend of the x-direction force and the y-direction force is the same, and the axial force varies within a certain range. The stable cutting stage was selected as the effective cutting force, and the cutting force measured under each parameter is shown in Table 3.
image 3. The result of the range analysis is aimed at the axial cutting force.
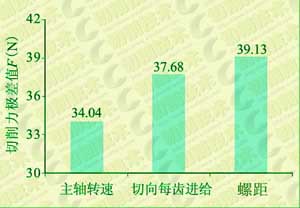
image 3. Extreme Difference of Cutting Force of Titanium Alloy
2.2 Influence of different processing parameters on aperture accuracy
The aperture accuracy is one of the important indicators of the quality of the hole. Have an important impact on the quality of the aircraft assembly and the service life of the components, The accuracy of the aperture machining under different parameters was studied by a three-coordinate measuring machine (see Table 4).
From the measurement results of the aperture, it can be concluded that the tolerance value of the titanium alloy hole processing is between IT5-IT7. In the fifth group, the aperture grade of processing parameters is IT5, and the aperture error is the smallest. The influence of processing parameters on the aperture is analyzed by the range analysis method, and the extreme difference obtained is shown in Fig. 4. Spindle speed and tangential feed per tooth are the main factors affecting the bore diameter, and the pitch has less effect on the bore diameter.
2.3 Influence of different processing parameters on the roughness of titanium alloy parts
Roughness is an important factor in evaluating the surface quality of Ti-6Al-4V.
There are strict requirements for the assembly of the aircraft. The roughness of the hole wall obtained under different parameters is shown in Table 5.
Table 5 Orthogonal test roughness measurement
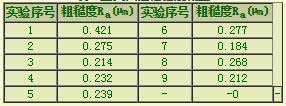
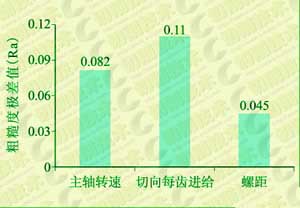
Fig. 5 Extreme Difference of Roughness of Titanium Alloy Parts
In the spiral milling process of titanium alloy parts, when the aperture roughness value is 0.18-0.42μm, the hole wall finish is excellent. The influence of the processing parameters on the roughness is analyzed by the range method, and the extreme difference obtained is shown in Fig. 5. It can be seen that the most important factor affecting the hole wall roughness is the tangential feed per tooth, followed by the spindle speed, and the least is the pitch.
In summary, the parameters are optimized to reduce the axial cutting force, reduce the aperture error, and improve the quality of the hole wall. The axial cutting force and aperture error of the fifth set of processing parameters are the smallest. The seventh group of parameters has the smallest wall roughness. Considering that the roughness value is far less than the aircraft manufacturing standard and the difference between the fifth group and the seventh group is only 0.055 micron, the fifth group of parameters is chosen as the optimal processing parameters for large diameter spiral milling holes.
3. The variation of the processing quality of large diameter holes of titanium alloy parts with the number of machining holes
Based on the above analysis, the variation of cutting force, machining quality and tool wear with the number of machining holes under the optimal machining parameters was studied.
3.1 Changes in axial cutting force
With the development of the aerospace industry, the application of titanium alloys has become more and more extensive, and the requirements for hole making precision and surface quality are getting higher and higher. At present, titanium alloy is not only an indispensable metal material in the aerospace industry, but also widely used in medical equipment and tools, metallurgy, shipbuilding and other industries. However, the titanium alloy has high strength, high hardness, low thermal conductivity, and the heat of cutting is not easily dissipated, resulting in serious tool wear, which seriously affects the service life of the tool, and the surface quality is poor and the efficiency is low. The tool movement during spiral milling is composed of three aspects: tool rotation, revolution and axial feed. The tool center is in a spiral path and is a process of drilling with a belt to facilitate chip discharge and heat dissipation (see Figure 1). This technology can greatly reduce the axial force, improve the quality of hole-making and improve the efficiency of hole-making. It can also easily realize "one knife and multi-path" by adjusting the eccentricity, which is favored by the aviation industry.
Kangding Company studied the special tool for spiral milling based on the principle of chipping, and analyzed the chipping effect of the special tool, the different cutting action of the end and side cutting edges and the service life of the tool. Perform finite element two-dimensional simulation of tools with different angle parameters to determine the appropriate tool angle range. The special tool for spiral milling is designed, and the dynamics of the spiral milling hole is studied. E.A. Rahim studied the effect of tool edge on the performance of the milling cutter. Jamal Ahnmad pointed out that the back angle of the spiral milling tool has a great influence on the cutting force. The cogging spiral milling cutter studied by Chatelian et al. has good cutting performance. The CFRP/Ti6Al4V process was studied, and the technological advantages of large pitch milling hole for processing laminated components were put forward. Li Dengwan optimized the processing parameters of titanium alloy by uniform design method, and improved cutting efficiency and surface quality. Chen Ertao established a machining parameter optimization model based on cutting parameters such as cutting speed, depth of cut and feed per tooth. Wang Fengchao studied the effects of different cutting parameters on the burr height, pore diameter deviation and roughness of the outlet.
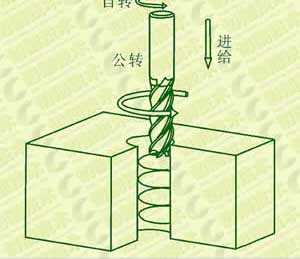
figure 1 Schematic diagram of TC4 titanium alloy spiral milling hole
In the assembly of aircraft, the number of holes below 1/2" diameter is the largest, so the research on spiral milling technology is mostly concentrated here. However, there are a certain number of large diameter holes in the key bearing parts, which is very difficult to process. At present, large-diameter hole processing usually uses multiple processes such as drilling, expanding, and reaming. The process is complicated, it requires dozens of tools, the processing cost is high, and the processing efficiency is extremely low, which has always been one of the difficulties in aircraft assembly.
Take a 12mm diameter spiral milling cutter as an example. The method of orthogonal milling and extreme value analysis was used to study the 19.05mm (3/4") large diameter spiral milling process of titanium alloy. The influence of different parameters on the processing quality was analyzed, and the optimal processing parameters were optimized. The research is beneficial to promote the application of spiral milling holes in the processing of large diameter holes, and it is also important to improve the efficiency of aircraft assembly and reduce the processing cost.
1. Test equipment and test design
Table 1 Physical properties and mechanical properties of titanium alloys
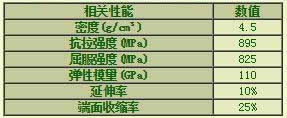
1.1 Test equipment and materials
The tool used in the test was an uncoated hard alloy spiral milling tool: The diameter is 12mm, the machining aperture is 19.05mm, the helix angle is 35°, the rake angle is 8°, the back angle is 15°, and the number of cutting edges is 4. The dry cutting method is adopted. The test workpiece material is a titanium alloy sheet with a thickness of 5 mm and a size of 120×250 mm. The physical properties and mechanical properties of titanium alloy are shown in Table 1.
The machining center is DMC75Vlinear five-axis CNC machine tool. The cutting force was measured by a three-way Kistler 9257A dynamometer. The detected signal is transmitted by Kistler 5007A charge amplifier, collected by data acquisition card, and displayed in real time by Dynoware dynamometer software. Aperture detection was performed using a Wenzel LH65 coordinate measuring machine, and four-point sampling was performed for each well to obtain aperture data; The roughness measurement was performed using a Mitutoyo roughness tester, and the tool wear was observed with an ultra depth microscope.
Table 2 DMC75Vlinear five-axis CNC machine tool orthogonal experimental parameter table
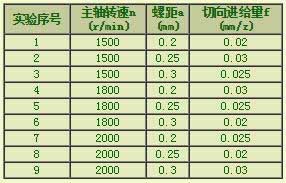
1.2 Ti-6Al-4V process cutting test design
Machining 3/4 (19.05 mm) holes with 12 mm large diameter cutter. The specific experimental parameters of three-factor and three-level orthogonal test are shown in Table 2. Among them, the pitch represents the downward feed distance of the tool per revolution, and the tangential feed per tooth represents the tangential cutting thickness of each cutting edge. Two wells were processed in each set of experiments and the measured parameters were averaged.
2. Test Results And Analysis
2.1 The influence of different processing parameters on cutting force
FIG 2 is a variation of the fifth set of cutting parameters measured under the condition of three-time curve of the cutting force, the axial cutting force is defined as the z-axis direction. It can be seen from the figure that the fluctuation trend of the x-direction force and the y-direction force is the same, and the axial force varies within a certain range. The stable cutting stage was selected as the effective cutting force, and the cutting force measured under each parameter is shown in Table 3.
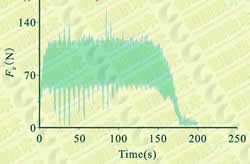
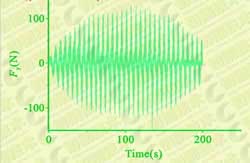
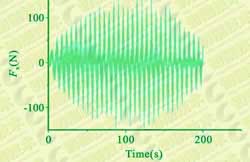
n=1800r/min, pitch α=0.25mm, tangential feed per tooth f=0.025mm/z
figure 2 Cutting force signal measured over time
figure 2 Cutting force signal measured over time
image 3. The result of the range analysis is aimed at the axial cutting force.
It can be seen from the figure that the pitch is the main factor affecting the axial cutting force of the tool, followed by the feed per tooth in the tangential direction. The minimum influence on the axial cutting force is the spindle speed.
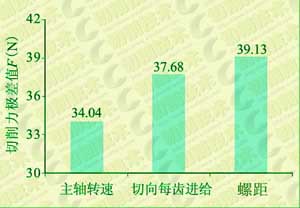
image 3. Extreme Difference of Cutting Force of Titanium Alloy
Table 3 Axial cutting force averaging test result
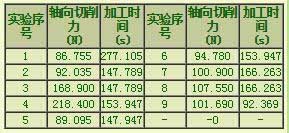
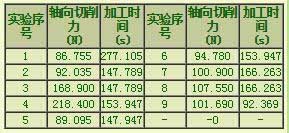
Table 4. Orthogonal test aperture measurement
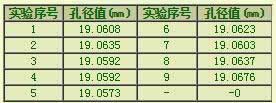
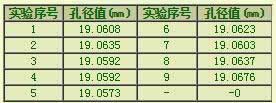
2.2 Influence of different processing parameters on aperture accuracy
The aperture accuracy is one of the important indicators of the quality of the hole. Have an important impact on the quality of the aircraft assembly and the service life of the components, The accuracy of the aperture machining under different parameters was studied by a three-coordinate measuring machine (see Table 4).
From the measurement results of the aperture, it can be concluded that the tolerance value of the titanium alloy hole processing is between IT5-IT7. In the fifth group, the aperture grade of processing parameters is IT5, and the aperture error is the smallest. The influence of processing parameters on the aperture is analyzed by the range analysis method, and the extreme difference obtained is shown in Fig. 4. Spindle speed and tangential feed per tooth are the main factors affecting the bore diameter, and the pitch has less effect on the bore diameter.
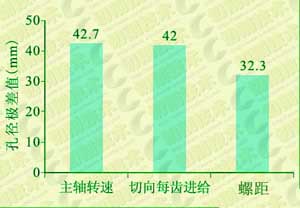
Fig. 4 Extreme difference of pore size of titanium alloy parts
2.3 Influence of different processing parameters on the roughness of titanium alloy parts
Roughness is an important factor in evaluating the surface quality of Ti-6Al-4V.
There are strict requirements for the assembly of the aircraft. The roughness of the hole wall obtained under different parameters is shown in Table 5.
Table 5 Orthogonal test roughness measurement
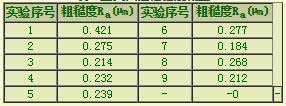
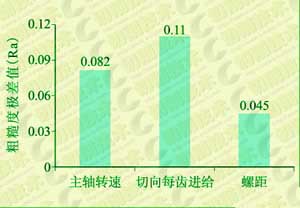
Fig. 5 Extreme Difference of Roughness of Titanium Alloy Parts
In summary, the parameters are optimized to reduce the axial cutting force, reduce the aperture error, and improve the quality of the hole wall. The axial cutting force and aperture error of the fifth set of processing parameters are the smallest. The seventh group of parameters has the smallest wall roughness. Considering that the roughness value is far less than the aircraft manufacturing standard and the difference between the fifth group and the seventh group is only 0.055 micron, the fifth group of parameters is chosen as the optimal processing parameters for large diameter spiral milling holes.
3. The variation of the processing quality of large diameter holes of titanium alloy parts with the number of machining holes
Based on the above analysis, the variation of cutting force, machining quality and tool wear with the number of machining holes under the optimal machining parameters was studied.
3.1 Changes in axial cutting force